Why Electric?
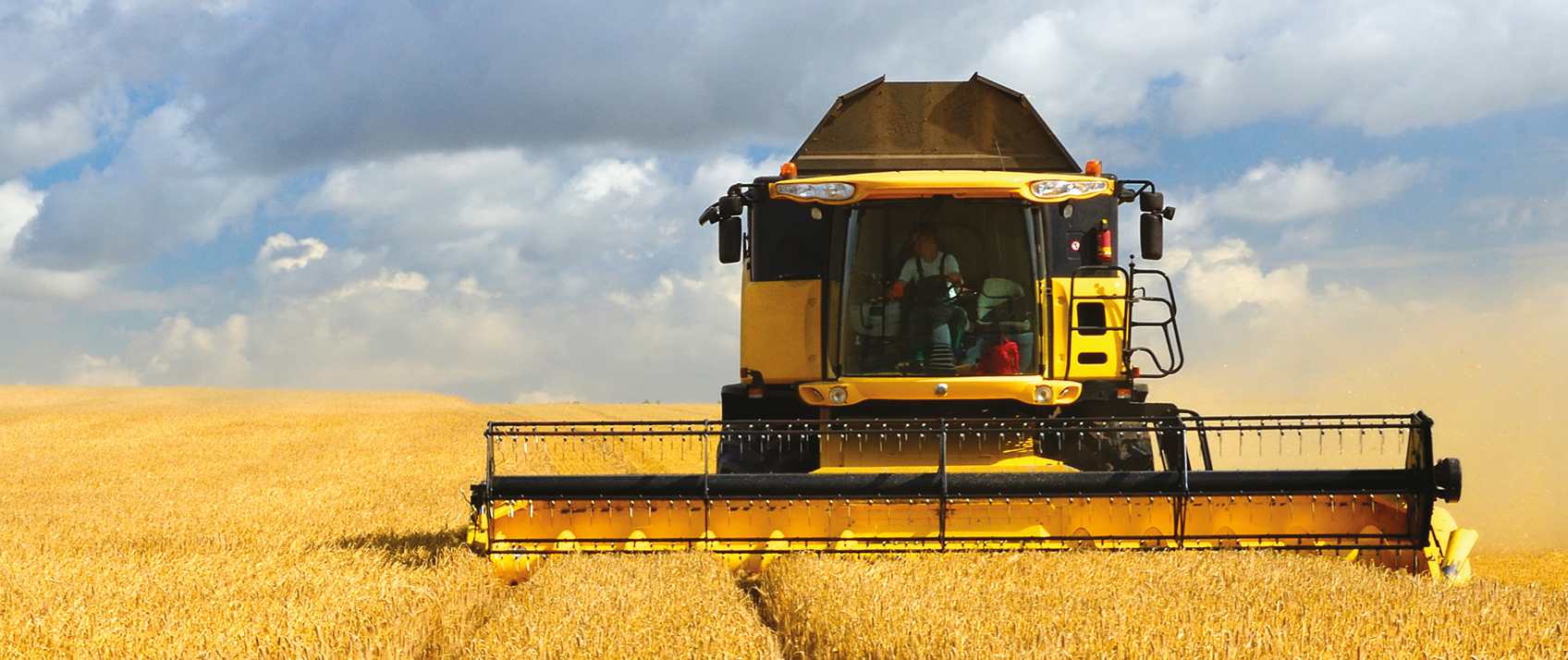
Two reasons: because in many applications, electric linear actuators can out-perform hydraulic and pneumatic, and because Thomson can make the conversion smooth and trouble-free for you.
Replacement with electric linear actuators is straightforward, and the long-term benefits are proven, including smaller component footprint; greater control and accuracy; lower maintenance costs; energy costs and noise; and more environmental sustainability all around.
Plus, Thomson smart actuators can communicate with a machine's electronic control unit (ECU), reducing the need for multiple single-function controllers. These actuators can accept commands and provide status information in return, such as position and speed and safety-related data such as load or temperature.
The value is clear. And as the originator of the electric linear actuator, Thomson has been helping mobile off-highway customers make a confident transition for more than 40 years. It's your turn to leverage these benefits:
Smaller footprint, simpler installation
- Quicker and more predictable system tuning than hydraulic
- Smaller footprint than hydraulic or pneumatic
- One electric actuator can replace numerous hydraulic or pneumatic actuators
- Quick two-pin installation
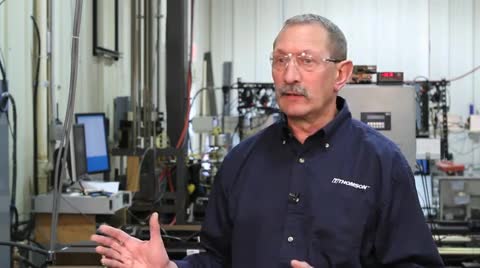
Better control
- Electric actuators operate with little force to reduce operator effort
- Joystick or remote control enables multiple motions, increased production and improved operator safety
- Multiple digital and analog feedback options
- Low-voltage switching options can interface with programmable PC/PLC controllers
- Pulse width modulation (PWM) for variable speed control
Better static load handling
- Holds power position when off – no pump required
- No drift when power is off
Higher accuracy
- Better positioning
- Better repeatability
- Instant reaction time to command (as opposed to hydraulic/pneumatic delay)
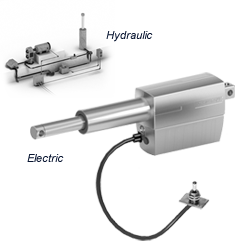
A single 2-wire/1-DPTP switch electric actuator can replace a complex hydraulic or pneumatic system, for significantly simpler design and implementation, better performance and lower lifetime costs.
Less maintenance
- No pumps, valves or hoses for fewer parts overall
- Self-contained unit eliminates access requirements for location flexibility
- No resizing or change-out to add components
- Programmable end-of-stroke limit switches for extended life
- No fluid maintenance necessary, no leak repairs
Lower overall system cost
- Longer component life
- Redundancy through manual overdrive
- Battery-run, no parasitic power draw and no system upsizing needed
- No pump operation or current consumption to maintain position, as electric only consumes power when moving a load
Less noise
- No pumps, air pressure or fluids means smooth, quiet operation
- No sound when cylinder is not moving a load
Cleaner environment
- Less overall power required to move a load
- No fluids, chemicals or solvents ever necessary: no environmental contamination or leakage
- Compact design is leaner to manufacture
- Regional manufacturing reduces carbon footprint
Make the smart switch to electric linear actuators. Thomson can make it happen.