How It Works
The unique design of the Glide Screw™ allows it to handle both axial, radial and moment loads without additional guidance. The result is an efficient and space saving design that is quick and easy to install with reduced maintenance needs compared to traditional solutions.
Watch this video to learn more about how Glide Screw can simplify your production needs.
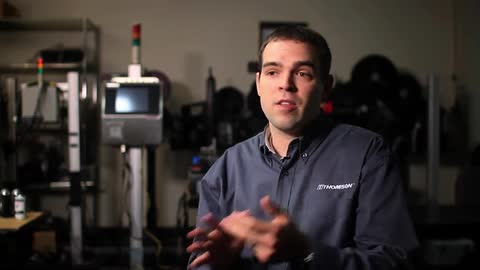


End Support
The choice of an end support method allows you to select the diameter needed for your application.
Fixed end – an end support that utilizes a support journal that has a length at least 2× the journal diameter (such as dual ball bearings).
Supported end – an end support that uses a single ball bearing, a plain bearing, or a bushing.
End support configurations
- Supported / supported
- Fixed / supported
- Fixed / fixed
Moment Load and Radial Load Charts
The Glide Screw is designed to actuate a moment load or a side load without additional linear guidance or support. Therefore, the screw deflection is the determinant feature and the following charts must be used to properly select a Glide Screw for an application.
Determine your end support configuration and use the following charts to properly select the nominal diameter of the Glide Screw. Select a product diameter that lies above and / or to the right of the design moment or load.
The lead of a Glide Screw is defined as the axial distance traveled for one revolution of the screw. Select the appropriate lead of your screw based on the desired speed and resolution of travel. (Note that the Glide Screw is limited to 300 RPM.)
